"Can carbon fiber parts actually be manufactured to be lighter, stronger, corrosion resistant and still cost 10%, 20%, even 30% less cash than aluminum and steel?"
I recently had the opportunity to interview Anthony, the Chief Composites Engineer at LeapTech Composites. With over three decades of experience in the field of Composites Engineering, Anthony’s expertise is highly sought after. After a bit of effort, I managed to pull him away from his computer models and analysis of captivating carbon fiber projects for a candid conversation. He graciously shared concrete insights and evidence to address the following inquiries. Keep reading, as it might be a while before I can command his attention again.
Interviewer: LeapTech places great emphasis on ensuring that each project leaves lighter than its initial state. Many incoming projects are crafted from steel or aluminum. How can you confidently assert that the carbon fiber alternative will be not only lighter but equally if not more robust?
Anthony: What often goes unnoticed is that conventional steel or aluminum components involve roughly a 50% material wastage. Carbon fiber enables us to conduct a stress analysis, pinpointing precisely where material is necessary to bear the weight load. This judicious material application not only minimizes weight but also capitalizes on carbon fiber’s inherent lightness. Typically, carbon fiber parts weigh 70% less than their steel counterparts, 50% less than aluminum equivalents, and 30% less than fiberglass options. For those seeking a direct comparison with their existing components, I encourage them to reach out at 877-696-4455.
“LeapTech took the doors from my Grand National, which is the second fastest in the world, and reduced the weight from 97 lb’s each to 33 lb’s each. Switching to Carbon Fiber doors is going to allow me to distribute weight in more beneficial places and will most likely take me to number one in the world.” -L.Hilliard
Interviewer: Considering the reduced material usage, does the use of less material limit your design possibilities or the scope of your creativity?
Anthony: Not at all, absolutely not. The key is to strategically place the material where the load will be applied. This approach allows for flexible and versatile designs while maintaining structural integrity. Moreover, carbon fiber possesses an aesthetic appeal that conveys cutting-edge technology, translating into increased value for your product and greater profitability.
Interviewer: Once a product is reimagined with carbon fiber, how can you ensure its durability in real-world conditions?
Anthony: (Chuckles) Carbon fiber has undergone extensive real-world testing, surpassing scrutiny more than any other material. Rigorous studies have explored aspects like corrosion, crack propagation, a wide array of stress factors, and thermal and electrical conductivity. The results clearly demonstrate carbon fiber’s superiority over steel and aluminum. It resists corrosion, displays minimal fatigue (far less than most metals), and exhibits a natural ability to halt crack propagation.
Interviewer: Carbon fiber sounds impressive so far, but what about its thermal conductivity? Given its dark color, I imagine it heats up quickly.
Anthony: Interestingly, carbon fiber exhibits low thermal conductivity and effectively conducts both heat and electricity. Allow me to present a hands-on challenge. Place a carbon fiber pole alongside a steel one in the scorching summer sun for an hour. Afterwards, you’ll find the carbon fiber pole is the one you can hold onto for a longer duration.
These snowmobile brackets came in made out of steel. We then altered the shape a little and only put material where needed to bare the weight load. Not only did this part come back beautiful and lighter it showed no deflection at 1000lbs when tested against the steel part which did have some deflection. -Snowmobile Racing Team
Interviewer: I’ll take your word for it, given your expertise. You’ve made compelling points, yet I’ve heard that carbon fiber is cutting-edge and expensive. How do you manage to produce products more affordably than steel or aluminum?
Anthony: While it’s not a universal rule, carbon fiber tends to be more cost-effective in about 90% of cases. As mentioned earlier, we employ just the necessary materials to create a structurally sound carbon fiber component. Additionally, our manufacturing approach allows us to consolidate parts, reducing assembly requirements. This not only saves time and reduces labor and material costs, but the true advantage lies in what I’m about to reveal. The superior fatigue resistance and crack prevention translate to fewer returns or replacements for customers. Satisfying customers and staying aligned with the latest technological advancements is a win-win. For instance, the Coast Guard recently decommissioned its first-generation composite boats after 60 years of coastal defense. This decision wasn’t due to structural issues, but rather to update hull designs and outdated onboard equipment. Carbon fiber’s enduring performance has been demonstrated over time, with a curious trait that its strength seems to improve over the years.
Interviewer: It’s truly remarkable—no concerns about corrosion or burns, coupled with lightweight, robust, and visually appealing components, all at a cost-effective price. It’s amazing how carbon fiber has turned out to be such a game-changer. Now that we’re all on board with its merits, how can one embark on the journey of reinventing their product using carbon fiber?
Anthony: You’re absolutely right, carbon fiber’s potential is indeed game-changing. Transitioning to carbon fiber involves a few key steps. First, identify the specific component or product you wish to reimagine. Second, collaborate with experts like us who specialize in composites engineering. We’ll work closely with you to assess design requirements, stress points, and material distribution to ensure optimal performance. Then, utilizing advanced techniques, we’ll craft the carbon fiber version of your product, maximizing its potential. This process might entail creating prototypes and conducting thorough testing to validate its capabilities. Throughout this journey, open communication and a shared vision will be crucial to bring your carbon fiber product to life successfully.
After receiving our carbon fiber planks we thoroughly tested them and found that they were better than our steel planks by leaps and bounds. Also the planks started out as 6 pieces welded together but with carbon fiber we combined all 6 pieces and made one continuous mold therefore you get a solid finished product made from carbon fiber.
-S. Abrahm
Now that you’ve read this interview, pick up the phone and call 877-696-4455 to see how carbon fiber can improve YOUR product. 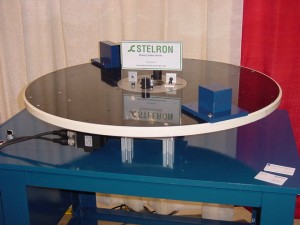
“LeapTech manufactured a series of dial tables for my manufacturing company I was ecstatic with the outcome. LeapTech’s carbon fiber rotary indexer table lowered the weight of my table by 329lbs (85% weight reduction). It increased production by 45% and saved us gobs of money on the smaller indexer we are able to run now. Amazing value!”
By the time you finish reading this article you will know how to improve your product with the amazing benefits of carbon fiber WHILE SAVING MONEY. Clearly you like what you’re reading about carbon fiber, because your still interested so let’s take it to the next step.
STEP 1:
Call (877-696-4455) or email LeapTech and let us know about your product and the problems you currently have. We’ve heard it all:
- We can’t move our products around easily and someone might hurt their back!
- Certain demographics are unable to lift our product with ease and always return it!
- My product has been around for quite a while with no new innovations and my competitors are leaving me behind!
- I want my product to look like it’s a 21st century product. If it doesn’t stay with the times people will stop buying it for new technology and I’ll be out of business.
- Business has been great this year and I need to increase production speed!
- Metal corrodes in our factory and I replace it every darn year!
STEP 2:
Once I understand what your product is all about I can put together a little estimate for engineering and best guess of what it will take to get you in the 21st century. Once you see how great the savings are we can begin the composite engineering process. Imagine your product weighing less, being stronger, looking amazing and costing less! Think about the unbelievable marketing opportunities with such a light and strong product! You’ll be provided with all of the amazing drawings, videos, numbers and analysis that we perform on your product. We will be able to tell you:
- -The amazing weight savings your product will see from switching to carbon fiber
- -The amazing price savings of composite products
- -Our models will show original tech information you’ve probably never dreamed of having for such a low price
- -We can even do a digital image of how great your product looks in carbon fiber!
Once the engineering is finished we move into creating an amazing prototype for you to show off. Now you know how pain-free the process is, you know the amazing characteristics of carbon fiber and you know we have the experience and resources to take YOU to the next level. Don’t wait any longer! Call us now to get started revolutionizing your ideas!
- Call 877-696-4455 now to increase the strength of your product and lower the weight up to 70%
- Click here to email us your drawings for modeling the new amazing characteristics of your part in carbon fiber
- Click here to learn more about how LeapTech will use our engineering experience and resources to revolutionize your product or part